A fast, affordable prefab build in Kent
This modern modular home was the quickest build ever seen on Grand Designs
In 2019 while watching Grand Designs: The Streets, Rob and Kate Harris saw a house made by a modular construction company called Boutique Modern. The firm builds homes from timber-and-steel boxes that are assembled at speed in a factory.
Each one is kitted out on the production line with everything from kitchen cupboards to light switches before being delivered to site on the back of a lorry and craned into place.
‘The idea that a house could be completed in a matter of weeks intrigued us,’ says Kate. Warehouse operative Rob, 58, and Kate, 47, who is a paddle sport instructor, had both grown up in the Tunbridge Wells area of Kent and were living near the town in a prefabricated home – albeit a rather dilapidated one dating from 1948.
On the fringes of a farm that was once owned by Rob’s family, their uninsulated bungalow was part of the government’s drive for emergency housing after World War II, and when the couple moved in during 2013 they knew the property was on borrowed time.
‘It was freezing, the windows were falling out and the roof was a patchwork,’ says Rob. ‘We wanted to replace it with a more comfortable house overlooking the landscape we’ve known all our lives.’
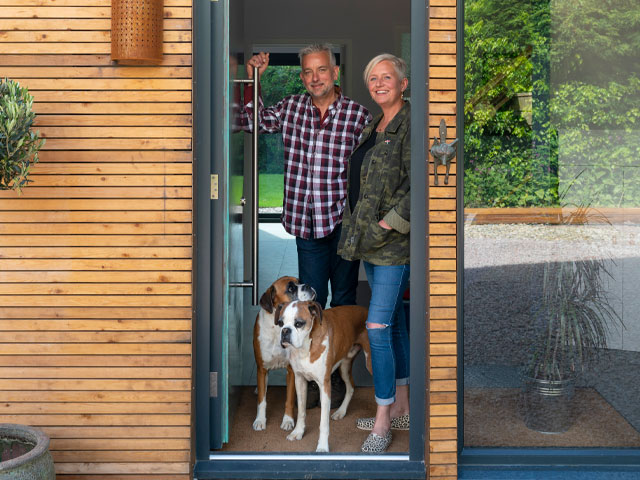
Kate and Rob in their Grand Designs prefab in Tunbridge Wells, Kent. Photo: Photo: Jefferson Smith
But the couple didn’t want to put anything conventional in its place. ‘It never crossed our minds to build something ordinary,’ says Rob. ‘At first we thought about using shipping containers, but my enquiries came to nothing.’
They were also aware that building a home doesn’t always go smoothly. ‘We’ve watched enough episodes of Grand Designs to know what can go wrong with self-builds,’ says Rob. ‘As Kate and I have no construction experience, we decided that a house made off site would be an easier and quicker option than building in situ.’
Based in nearby Newhaven, Boutique Modern is the brainchild of Dick Shone, an artist who used to work in product development at Ikea. ‘We build architect-designed houses using time-tested materials and methods,’ he says. ‘The joy of modular construction is that everything happens in a controlled environment.’
‘The modules are designed down to the last nut and bolt and we use data analysis from previous projects to calculate precisely how long it will take and how much it will cost.’
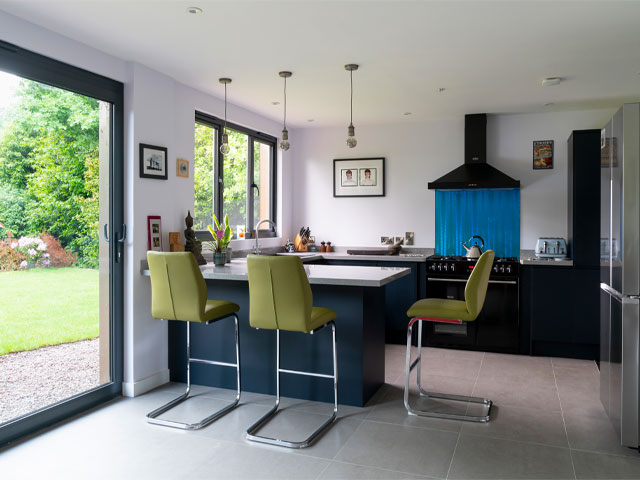
The modern kitchen. Photo: Jefferson Smith
Though the company specialises in affordable housing, it also takes on occasional self-builds such as the one Rob and Kate had in mind. To settle on a bespoke design, Dick, Rob and Kate started playing around with some small plywood blocks, each of which represented one section of the house. They arranged six modules, four on the ground floor and two on top, because Rob and Kate had always wanted a bedroom opening out on to a roof deck.
‘When Dick suggested slightly rotating the top section it blew our minds,’ says Rob. ‘This is how our bedroom ended up at a different angle from the rest of the house.’ In 2021 an inheritance provided the funds the couple needed to get started, and their home began its 15-day journey through the factory.
Boutique Modern oversaw the demolition of the old prefab, a process that took longer than building the house because it contained huge amounts of asbestos. It also prepared the site with 18 concrete pads on which the new structure would stand. After being assembled in tightly controlled conditions, delivering the house to the plot is the trickiest phase because suddenly things become much less predictable.
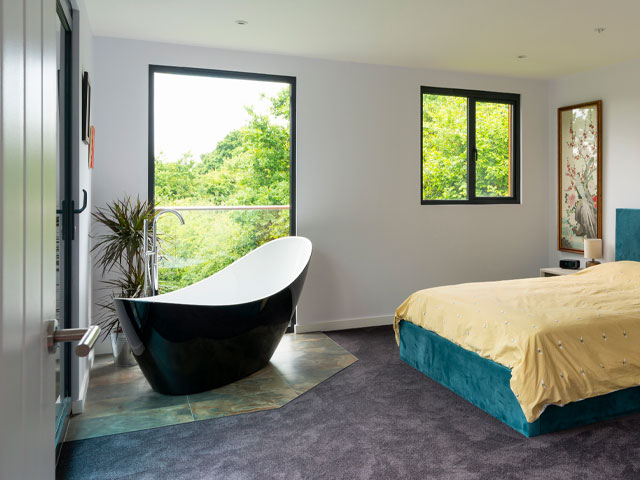
The master bedroom. Photo: Jefferson Smith
Sure enough, it was at this point that the neighbouring landowner, worried about possible damage from lorries and cranes, withdrew access permission. Once this was resolved through a financial settlement, the installation went like clockwork and all six modules were put up in just two days.
The team bolted them together and connected the plumbing and electrics, after which the structure was insulated with a thin layer of silicone dioxide before being wrapped in Corten steel and larch. The house is just 25 per cent bigger than the 1940s prefab, but the interior, with its open-plan living area and three bedrooms, is much warmer, brighter and more eco-friendly.
‘We adopt a fabric-first approach, choosing high performing materials to make the structure airtight and well insulated,’ explains Dick. ‘This minimises the need for heating and cooling. Modular construction can also be more sustainable than a conventional build because the precision-engineering reduces waste.
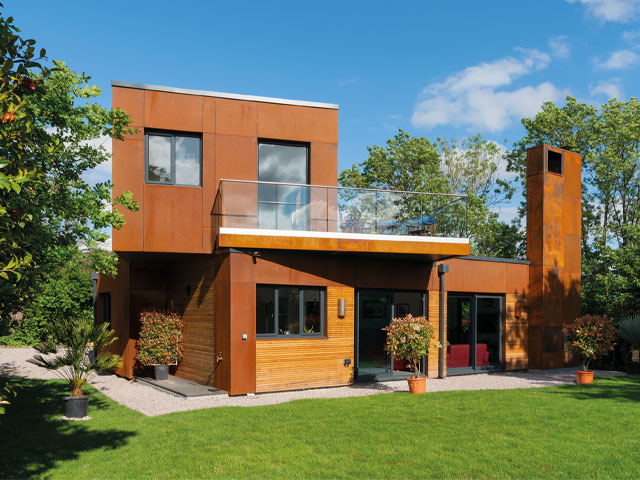
The Tunbridge Wells prefab is clad in Corten steel and timber. Photo: Jefferson Smith
‘We salvage all offcuts and reuse every spare screw,’ says Dick. The couple’s original £350,000 budget overran by £20,000, partly due to the £5,000 access payment, but also because Building Control unexpectedly asked them to install a sprinkler system. Rob and Kate also chose to spend more than they had planned on a suspended wood burning stove and copper front door.
‘But even with these extras, we couldn’t have built this house in the normal way for the same price,’ Rob says. ‘The whole experience was a whirlwind, but we loved it from start to finish,’ says Kate. The finishing touch came when Dick presented them with a house manual, accessed via a QR code, giving advice on everything from replacing lightbulbs and retouching paint colours to weeding the green roof.
‘Our build was incredibly easy,’ says Rob. ‘We didn’t spend months on a muddy building site and we ended up with exactly the home we wanted, in the place we love.’